See this junk covered table? It's the smaller of two production tables and is supposed to be where we personalize our completed designs. I say supposed to because it's been months since it's been used that way. This table is a quick chair roll away from my desk, giving me easy access to it. Which means this is where I pile all manner of junk. My production manager, Nicole, is very gracious about this. She has reconciled herself to working in a fraction of the necessary space and not once has complained about it.
Nicole has been with me for more than 5 years. She literally runs the show. I could die tomorrow and unless you'd read about it in the paper, you'd never know. She'd just keep on cranking out pottery without blinking a teary eye. She's fricken awesome.
This incredible woman has helped me grow Museware Pottery from a one woman show to a leader in the hand painted, personalized pottery industry. Over the years, Nicole has watched me revel in great delight as we've grown & collapse in despair when we nearly closed back in 2008. Every step of the way, she's been right by my side - my biggest fan and supporter.
The point is that no matter what I do, good or bad, on task or so totally off that anyone else would be searching for an ice pick, Nicole is right behind me. So back in January, when I started getting that starry look in my eyes and decided we were opening a showroom & gift shop - she didn't flinch. She ran around cleaning up behind me, bringing me coffee and feeding me lunch while I ran around like Chicken Little. Renovating the studio to make room for this big dream was expensive and time consuming. I was a little bit psycho and a lot stressed out, which means I was not always on my best behavior. Our new showroom opened April 19th, nine days after my 57th birthday. I felt more like 87. The 80+ smiling people who came to our opening loved our new place. Completely worn out, I found a chair and watched it all unfold.
Because I become so possessed, the completion of any big project always leaves me slightly adrift. I wander around listlessly, lost for purpose and feeling deflated. Without direction, I came in late and left early for an entire week. Sigh. I'd rendered myself redundant.
I started this blog on April 26th - a week after our opening. All it took was a single image of a
Galbraith & Paul fabric stamp. Once I'd seen it, my new purpose & product line was determined. Once again, I was a woman on a mission.
Painting fabric takes a lot of space. And if there is anything we are short of around here, it's space. Every corner of every room is stacked with stuff. Stuff we need. In a way that only The Boss can, I started eyeballing Nicole's table. Because she's my loyal rock, she began colluding with me.
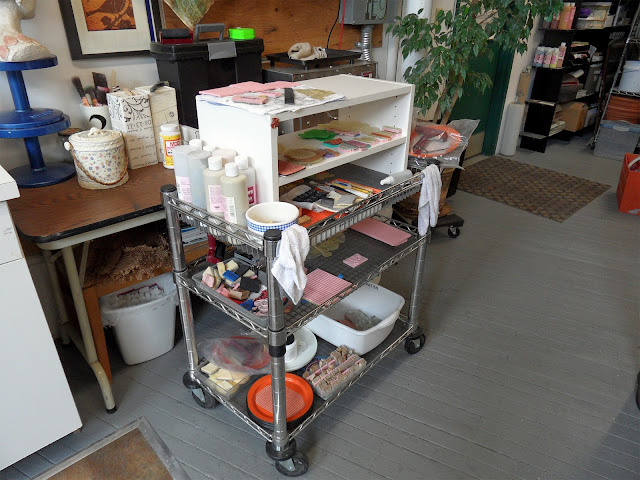
See this cart? We call this fabulous little invention the EMPU (em-pew.) Our new Emergency Painting Unit houses our fonts, our most commonly used stamps, paint, cleaning stuff - everything needed to personalize every item in our line. It is one of the biggest improvements we've made to our process since we automated ordering last November (totally eliminating Leslie's job.) Because the personalization table was so cluttered with {my} junk, there was no room to actually paint on it. Nicole would stamp out the main design on the big table then stack everything on a cart, roll it over to personalization, do the damn thing, stack it back on the cart then roll it back over for glazing. Huge. Waste. Of. Labor.
Now, instead of juggling and potentially damaging plates, Nicole drags EMPU around the main table. She is practically giddy with pride and smiles every time she walks past it. And I smile each time I walk past my new, 5 x 8' block printing table. It's still heaped with junk and will be until I'm ready to wrap carpet padding with muslin and start printing me some fabric.